In the ever-evolving world of fleet and vehicle graphics, staying ahead of the curve means understanding and leveraging the latest technological advancements. One such innovation is Arlon Graphics’ FLITE Technology. Known for its ease of use and superior performance, FLITE Technology is revolutionizing the way graphics are applied to vehicles and fleets. Here, we delve into the practical applications of FLITE Technology and share some valuable tips and tricks for maximizing its benefits.
The Benefits of FLITE Technology
1. Effortless Liner Release:
FLITE Technology features an easy liner release that simplifies the installation process. Unlike traditional methods that often require two installers, FLITE Technology allows for a smooth, distortion-free application by a single installer. This ease of use is especially beneficial when precise registration between panels is critical.
Tip: To take full advantage of the effortless liner release, start by peeling back a section of the liner to position the graphic and establish a stable hinge. You can then remove the entire liner with confidence that because of FLITE Technology, you will have perfect placement without stretching, creasing, or distorting the graphic.
2. Unmatched Repositionability:
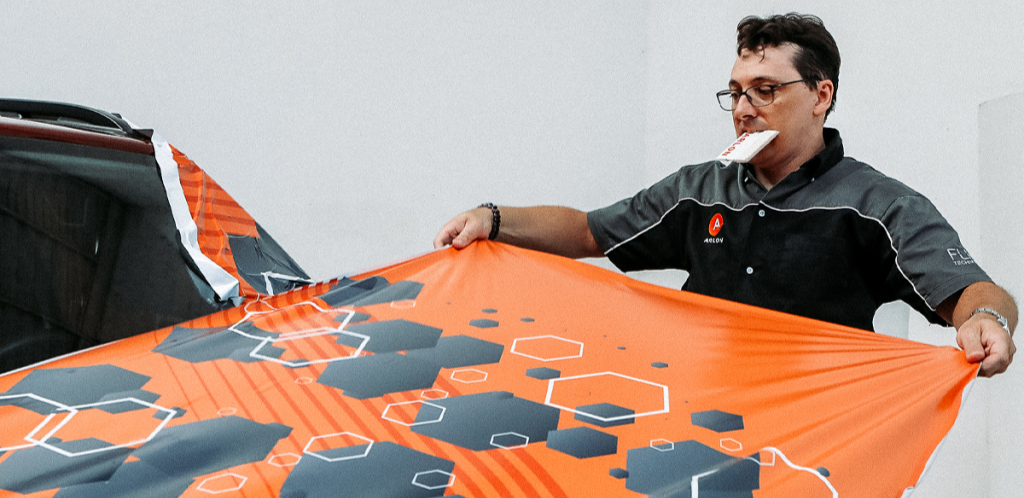
One of the standout features of FLITE Technology is its ability to be repositioned easily. The film “floats” over the vehicle’s surface until firm pressure is applied, allowing entire panels to be realigned even after the liner is removed.
Tip: If you encounter a wrinkle or crease during application, gently lift the graphic and reapply. This flexibility prevents over-stretching and ensures a flawless finish, even in challenging areas like deep channels and contours.
3. Bubble-Free Installs:
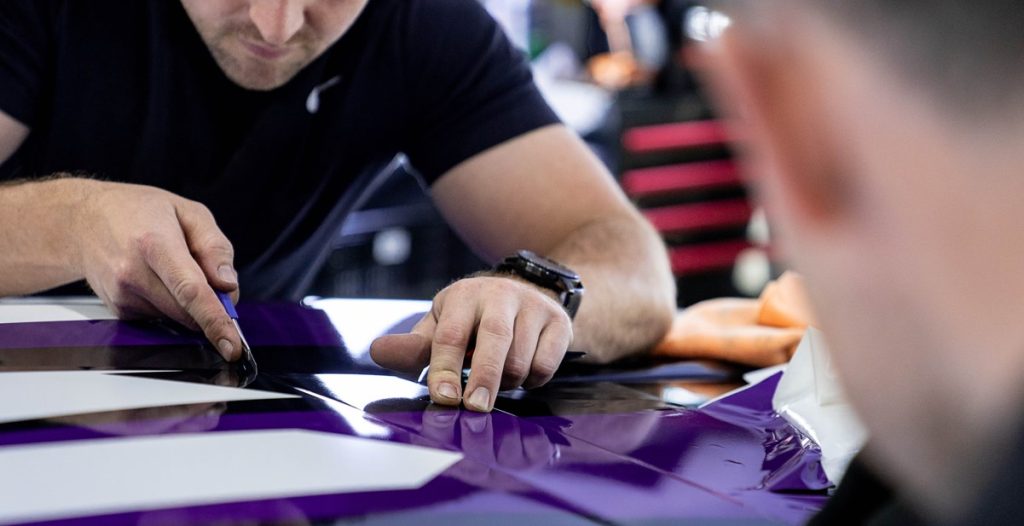
FLITE Technology’s low initial contact minimizes air entrapment, making bubble-free applications a breeze. Should any bubbles appear, they can be easily removed by applying gentle pressure to move the air pocket to the edge of the graphic.
Tip: Press directly over the bubble with your thumb and work your way outwards to ensure a smooth, bubble-free finish.
4. No Glue Dots:
The topography-based adhesive system of FLITE Technology reduces the contact percentage with the substrate without the use of inhibitors, hence, preventing the formation of unsightly glue dots.
Tip: For solvent prints, let the film outgas sufficiently before lamination and ensure that the substrate is clean and free from dust or debris before application. For optimal performance, apply the film in a climate-controlled environment.
5. Redefining Ultimate Bond:
FLITE Technology achieves a strong bond with the substrate when post-heated, without the need for primers or adhesive promoters. This high bond strength ensures the graphic stays in place, even in the most demanding conditions.
Tip: Use a heat gun to post-heat the graphic, especially in deep channels and recessed areas. Ensure consistent heating and reapply pressure on the film to secure the bond effectively.
Practical Applications in Fleet and Vehicle Graphics
Fleet Wraps:
For fleet managers looking to maintain a consistent and professional appearance across their vehicles, FLITE Technology offers a reliable and efficient solution. Its repositionability and bubble-free installation ensure that graphics can be applied quickly and accurately, minimizing downtime and maximizing fleet visibility.
Vehicle Customization:
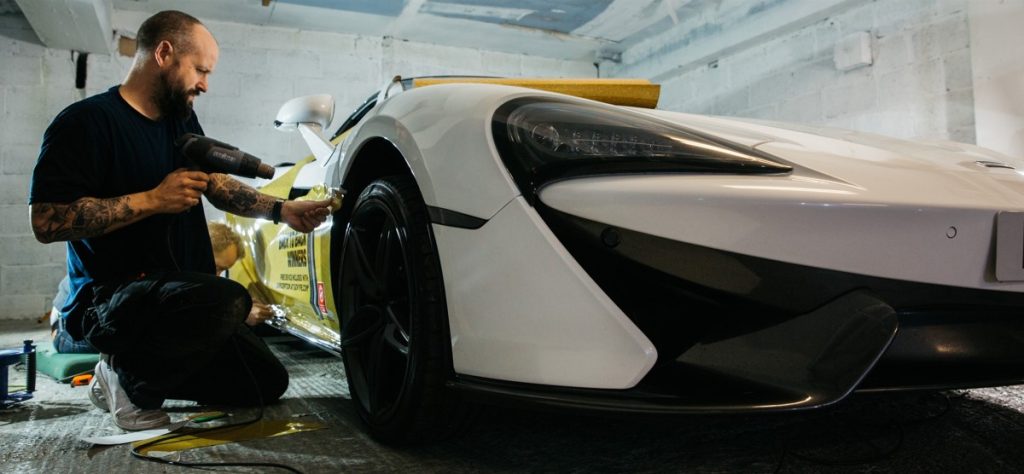
Whether for commercial or personal use, vehicle customization is simplified with FLITE Technology. The easy liner release and ability to reposition graphics make it an ideal choice for applying intricate designs or large panels single-handedly.
Arlon Graphics offers a variety of products tailored for vehicle customization:
SLX® Cast Wrap and SLX+®: These industry benchmarks are renowned for installation speed and efficiency. Integrated with FLITE Technology, they provide unmatched repositionability and long-lasting performance, making them ideal for the most demanding applications.
Premium Colour Change films: Available in a selection of 40 colors, these films also feature FLITE Technology, allowing for fast, easy installation and excellent repositioning. This makes them perfect for those seeking to personalize their vehicles with vibrant, durable wraps. Please note that PCC is not sold in every region, so be sure to check availability in your area.
Reflective Graphics: Safety and visibility are paramount in fleet applications. Products like IllumiNITE Wrap® combine FLITE Technology with premium reflectivity, ensuring optimal visibility in low-light conditions. This enhances both the aesthetic appeal and safety of fleet vehicles.
Sustainable Options: For those seeking environmentally friendly solutions, DPF V9700 is a non-PVC cast film that reduces environmental impact without compromising performance. This film, equipped with FLITE Technology, provides easy installation and clean removal, ensuring durability and sustainability.
Conclusion
FLITE Technology, pioneered by Arlon Graphics, sets new fleet and vehicle graphics standards. Its innovative features not only simplify the installation process but also enhance the durability and appearance of vehicle wraps. By incorporating these tips and tricks, installers can achieve professional, long-lasting results with ease. Whether you’re a seasoned professional or new to vehicle graphics, FLITE Technology ensures that every project is wrapped right the first time, every time.